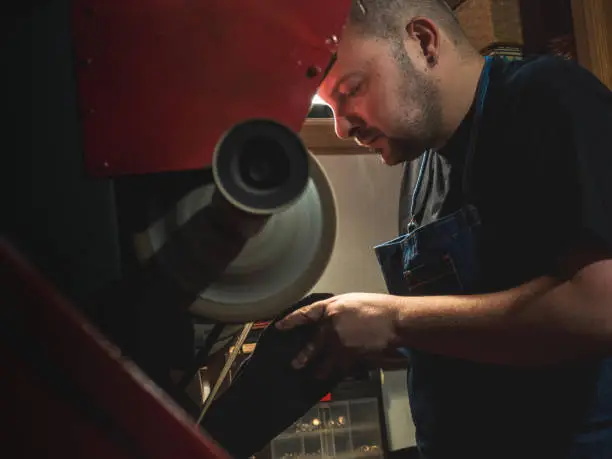
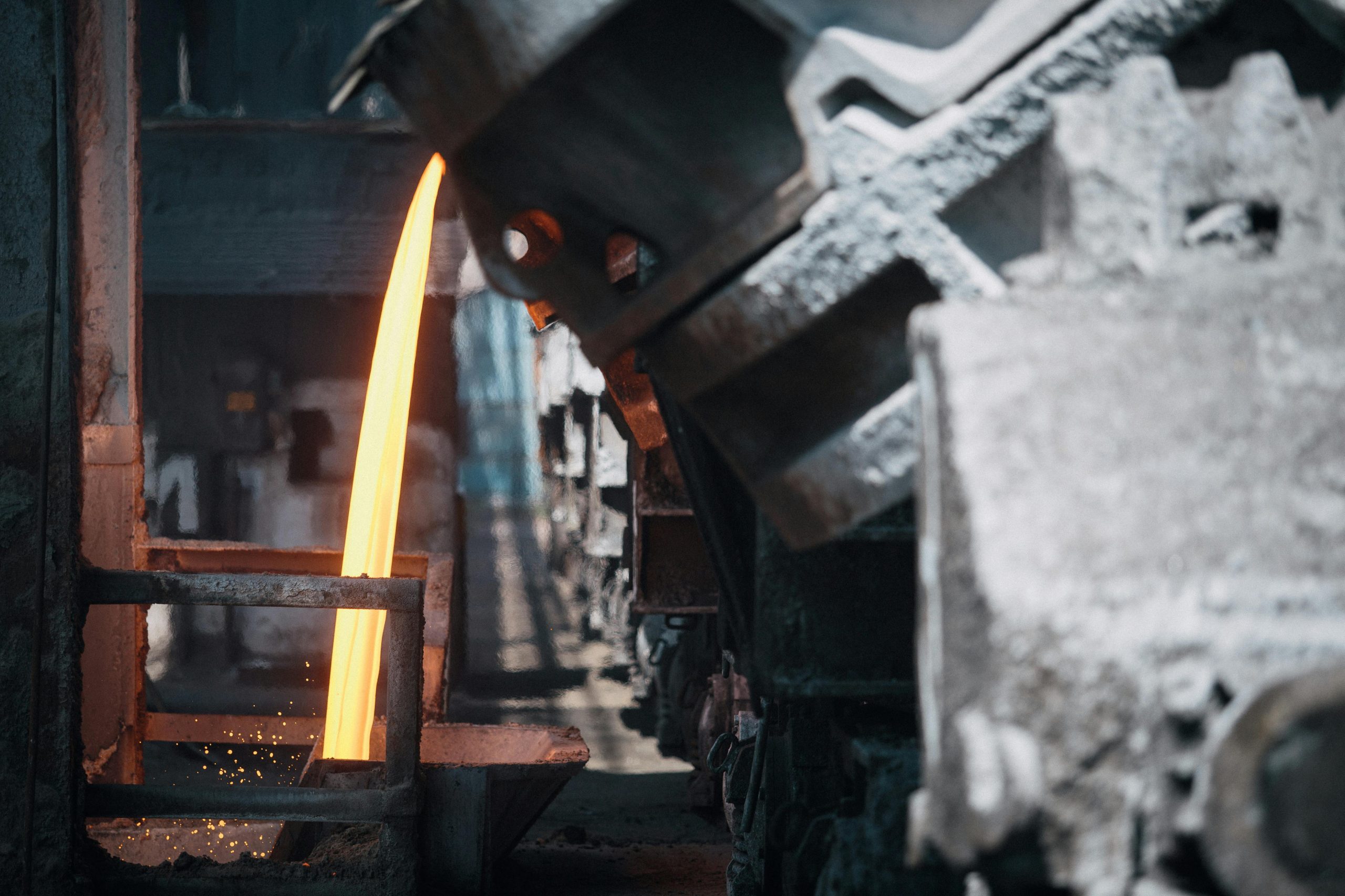
Pro’s and con’s of cold forming vs hot forming
Cold forming and hot forming are two widely used manufacturing processes in the industry. Both have their own advantages and limitations and understanding them is crucial for making informed decisions. In this article, we delve into the basics of cold forming and hot forming, explore their respective benefits and drawbacks, and provide insights on how to choose the right method for your specific requirements.
What is cold forming?
Cold forming, also known as cold working or cold forging, is a manufacturing process that shapes metal at room temperature. Unlike hot forming, which involves heating the material, cold forming relies on mechanical forces to change the shape and properties of the metal.
The process of cold forming typically starts with a metal blank that is fed into a die. The die is the desired shape which is then achieved thanks to pressure exerted by the roller. Cold forming is commonly used for producing components with high dimensional accuracy and complex geometries.
Cold forming has been a crucial technique in the manufacturing industry for centuries, allowing for the production of intricate metal components with precision and efficiency. The process not only shapes the metal but also enhances its mechanical properties, making it a preferred method for creating parts that require strength and durability.
The process of cold forming metal
The cold forming process begins with the preparation of the metal blank. The blank is usually made from low-carbon steel, stainless steel, or aluminium due to their excellent formability and mechanical properties.
Once the blank is prepared, it is rotated and shaped using force from a roller arm which is also rotating. The resulting deformation causes the atoms in the metal to rearrange, resulting in improved mechanical properties and increased strength.
After the metal has been shaped in the die, it undergoes further processes such as heat treatment or surface finishing to meet specific requirements. These additional steps ensure that the cold-formed part meets the desired specifications for its intended application, whether it be in the automotive, aerospace, or construction industry. Read more about the metal spinning process.
Materials used for cold forming
Not all materials are suitable for cold forming. Metals with high ductility and low strain hardening, such as mild steel and aluminium, are commonly used in cold forming processes. These materials can be deformed without significant cracking or failure, which is why it’s essential to select the right material for cold forming to achieve the desired results.
Factors such as the metal’s composition, grain structure, and mechanical properties play a crucial role in determining its formability and suitability for the cold forming process. Manufacturers often conduct thorough material testing and analysis to ensure that the chosen metal meets the required criteria for successful cold forming operations.
Advantages of cold forming
One of the lesser-known advantages of cold forming is its environmental impact. Unlike traditional manufacturing methods that produce a significant amount of scrap and waste, cold forming is a more sustainable option. The minimal material waste generated during the cold forming process not only reduces the environmental footprint but also contributes to cost savings for manufacturers.
Cold forming is a highly efficient process that minimises material waste. Since the metal is shaped at room temperature, there is no need for expensive heating and cooling equipment. Additionally, the high-speed production capabilities of cold forming result in shorter cycle times and increased productivity.
Furthermore, the versatility of cold forming allows for the production of complex geometries with ease. This flexibility in design capabilities opens up new possibilities for engineers and designers to create innovative components that may not have been feasible with traditional manufacturing methods.
Cold forming provides excellent surface finish and dimensional control. The process eliminates the need for additional finishing operations, such as machining or grinding, reducing overall production time and costs. The tight tolerances achieved through cold forming ensure precise and reliable component dimensions.
In addition to its cost-saving benefits, cold forming also enhances the mechanical properties of the formed parts. The process of cold working the metal increases its strength and hardness, resulting in components that exhibit superior performance characteristics. This improved mechanical behaviour makes cold-formed parts ideal for applications that require high durability and reliability.
Read ‘How to choose the best metal spinning method for your project’ for more specific insights into the possible applications of cold forming.
Potential limitations of cold forming
Cold forming is not suitable for all types of metals. Materials with limited ductility or high strain hardening, such as high-carbon steel or brittle alloys, may not be suitable for cold forming processes. It is important to carefully select the appropriate material for cold forming applications to ensure successful outcomes.
During cold forming, the metal can undergo work hardening, leading to increased strength but reduced ductility. This can limit the formability of the material and result in cracking or failure. Proper annealing or heat treatment processes may be required to restore the ductility of the cold-formed components.
Furthermore, another limitation of cold forming is the complexity of shapes that can be achieved. While simple geometries can be easily formed using cold forming techniques, more intricate shapes may require multiple forming operations or the use of additional processes such as machining. This can increase production time and costs, making cold forming less economical for complex components.
Moreover, the size of the components can also be a limiting factor in cold forming. Large or thick parts may require higher forming forces, which can result in increased tool wear and reduced dimensional accuracy. In such cases, skilled engineers and those with material knowledge will be able to compensate for this by making changes to the process.
What is hot forming?
Hot forming, as the name suggests, involves heating the metal to high temperatures before shaping it. The elevated temperatures make the material more malleable and easier to deform. Hot forming is a crucial process in the manufacturing industry. The method allows for the creation of intricate and structurally sound parts that may be challenging to achieve through cold forming techniques.
The hot forming process explained
The hot forming process starts with heating the metal to temperatures above its recrystallisation temperature. This temperature range depends on the type of metal used. Once heated, the metal is formed using various techniques, such as press forming or drop hammering.
During the hot forming process, the metal’s grains elongate in the direction of the deformation, aligning themselves to provide better mechanical properties in the finished part. This alignment enhances the material’s strength and reduces the likelihood of defects, resulting in components with improved performance characteristics.
Ideal materials for hot forming
Hot forming is commonly used for metals with low ductility at room temperature, such as high-strength steel and some alloys. The elevated temperatures reduce strain hardening and increase the formability of these materials, making them easier to shape into complex geometries. Furthermore, hot forming can improve the overall material properties by refining the grain structure and eliminating internal stresses. This process enhances the part’s resistance to fatigue and impact, crucial factors in applications where structural integrity is paramount.
Benefits of hot forming
Hot forming allows the production of components with intricate geometries and complex shapes. The elevated temperatures increase material ductility, enabling the formation of parts that would be difficult or impossible to achieve with cold forming methods.
Hot forming helps to minimise residual stresses in the material. The high temperatures promote uniform deformation, reducing the likelihood of cracking or distortion in the final component. This results in improved component reliability and longevity.
Another advantage of hot forming is its cost-effectiveness and efficiency in large-scale production. The process allows for faster production rates compared to cold forming, reducing manufacturing lead times and overall production costs. Additionally, the ability to form complex shapes in a single step can eliminate the need for multiple secondary operations, further streamlining the manufacturing process and reducing waste.
One of the lesser-known benefits of hot forming is the enhancement of material properties. When metals are heated to high temperatures during the hot forming process, the grain structure of the material can be refined, leading to improved mechanical properties such as increased strength and toughness. This can result in components that are not only more durable but also lighter in weight, making them ideal for applications where weight reduction is crucial.
Discussing the drawbacks of hot forming
Despite its benefits, hot forming also has some drawbacks that need to be considered, such as:
Hot forming requires significant energy inputs to heat the material to the required temperatures. The heating process can be expensive, especially for large-scale production runs. Additionally, the need for specialised equipment and additional heating facilities can drive up the overall manufacturing costs. In contrast, cold forming processes do not require extreme heat. You can read about this in more detail in our other post, ‘How to save costs with metal spinning’.
During hot forming, exposure to high temperatures can lead to oxidation and decarburisation of the material. Oxidation results in the formation of an oxide layer on the surface of the metal, while decarburisation reduces the carbon content in the material. Both can negatively impact the mechanical properties of the final component.
Another drawback of hot forming is the complexity of process control. Maintaining consistent temperatures throughout the forming process is crucial to ensure the desired material properties. Variations in temperature can result in uneven forming, leading to defects in the final product. This requires sophisticated monitoring systems and skilled operators to adjust parameters in real-time.
When using hot forming techniques, the choice of materials is limited to those that can withstand high temperatures without deforming or losing their properties. This restriction can be a challenge when specific material properties are required for the end product. Additionally, the high temperatures and pressures involved in hot forming can accelerate tool wear, leading to increased maintenance costs and downtime for tool replacement.
Cold forming vs hot forming: Making the right choice
The factors to consider when deciding between cold forming and hot forming, are the material’s formability, complexity of the component, desired mechanical properties, and production volume. Each method has its strengths and limitations, and selecting the appropriate one ensures optimal results.
Impact on final product quality
The chosen forming method will significantly impact the final product quality. Consider factors such as dimensional accuracy, surface finish, material strength, and overall part integrity when making the decision.
The cold forming technique is renowned for its ability to produce parts with excellent surface finish and dimensional accuracy. This method is particularly advantageous for high-volume production runs where tight tolerances are crucial.
On the other hand, the hot forming method allows for greater malleability, making it ideal for creating intricate and complex geometries. The heat involved in hot forming also aids in reducing residual stresses within the material, resulting in enhanced overall part integrity.
Metal forming process specialists
Ultimately, the type of metal forming that works best for you depends on your project requirements, material choices, and any other factors that are specific to the business or industry. The team at Tanfield Metal Spinners will be happy to discuss why certain forming processes are recommended, and this will be reflected in any quotes we provide. Get it touch if you have any questions.